STANDARD PCBS VS ALUMINUM
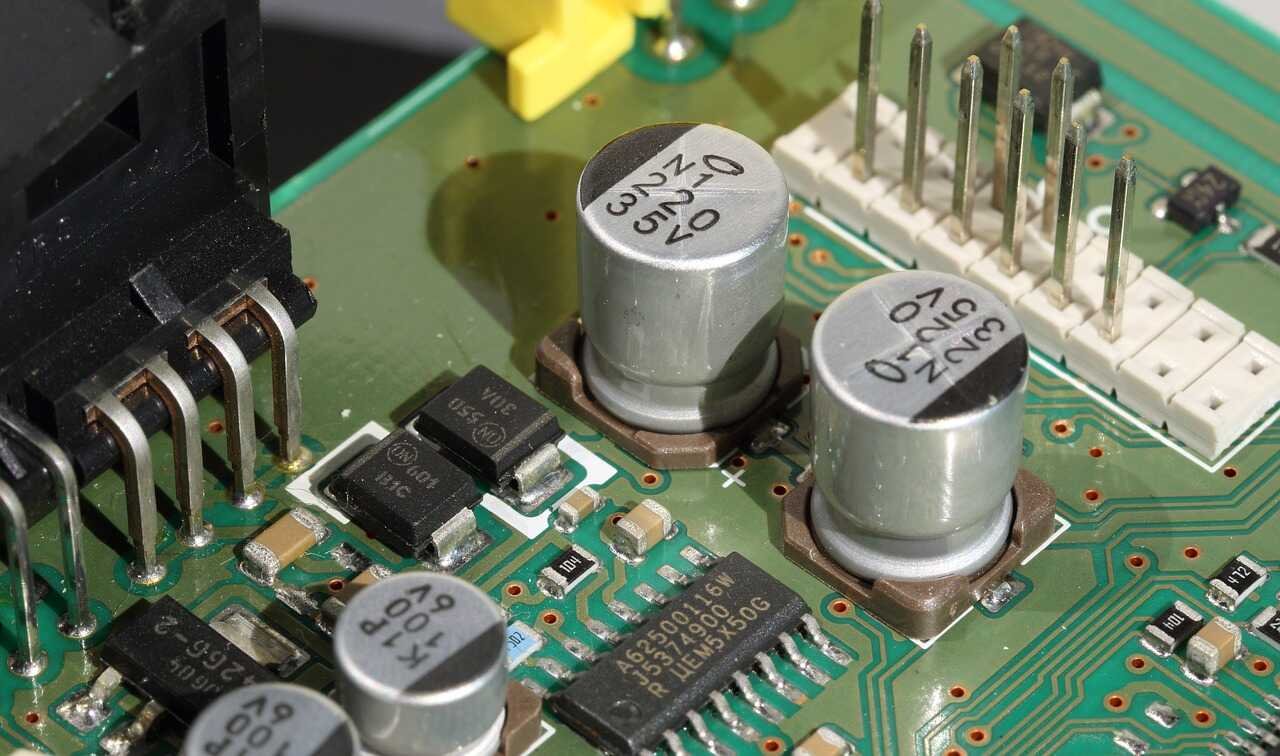
When it comes to PCB creation, every material counts. Boards with aluminum cores (aluminum PCBs) have different properties than boards without metal substrates (standard PCBs). Both types of boards are used in many commercial and consumer electronics products. Is a Flexible Aluminum PCB or a standard PCB better for your application? That depends on the application.
STANDARD PCBS: WHAT ARE THEY?
Copper is the most prominent metal on a standard PCB. There are several layers of copper on the board. The substrate, or base, is made from fiberglass, polymers, ceramics, or another non-metal material. FR-4 is a popular substrate for these PCBs. This fiberglass material is relatively affordable and has moderate durability. The board is made conductive and outlines component locations with copper, solder mask, and silkscreen layers. It is possible to have these layers on one or both sides of the base or stacked multiple times.
Standard PCBs are used for a wide range of applications. Materials and construction affect their capabilities, so they power both low- and high-end electronics. PCBs with a single side appear in less complicated devices such as calculators, while multilayer boards are used in aerospace equipment and supercomputers.
PCBS – ADVANTAGES AND DISADVANTAGES
The standard PCB is well-rounded and adaptable. Different substrate options affect the price and durability of the board. When your budget is limited and your purpose is low-intensity, fiberglass can be a cost-effective choice. However, if you are more concerned with the level of stress, you can invest in a stronger base material. Radio-frequency substrates and flexible substrates are good choices for special applications.
FR4 circuit boards, however, require extra components to maintain stability at high temperatures. Non-metal substrates lack thermal conductivity, so you must add a thermally conductive material. The circuits in your device may be prone to stress and damage if it has a high-power or high-density design. Heat must be directed away from the circuits using heat sinks, copper-filled vias, or forced air.
WHICH ARE ALUMINUM PCBS?
The layout of an aluminum PCB is similar to that of any other PCB. A layer of copper, a solder mask, and a silkscreen is layered over it. A metal substrate, however, is what an aluminum circuit board has, instead of fiberglass or plastic substrate. Aluminum is the primary component of this base. A metal core can be entirely made of metal or can be made up of a combination of metal and fiberglass. PCBs made of aluminum are usually single-sided but can be double-sided as well. It is very difficult to manufacture multilayer aluminum PCBs.
LEDs and power-converting electronics are the most frequently used aluminum boards. LEDs emit intense light that generates high levels of heat, which aluminum conducts away from components. With an aluminum PCB, LED devices are more stable and have a longer lifespan. The aluminum substrate can be found in street lights, stop lights, and household lighting. It allows currents to be converted and electronics to be regulated. Aluminum PCBs are also used by creators in many other industries, but they don’t implement them as often.
ALUMINALUMINUM: PROS AND CONS
Aluminum boards are among the most thermally conductive PCB options. As much heat as possible is kept away from critical components to ensure minimal circuit damage. Due to their high heat tolerance, they can handle higher-density circuits and higher power levels.
Aluminum alloys have a high level of physical durability, which reduces the risk of breakdown. Aluminum is a metal with low environmental impact and a reasonable price compared to other metals.