The 6 big benefits of choosing the right PLC
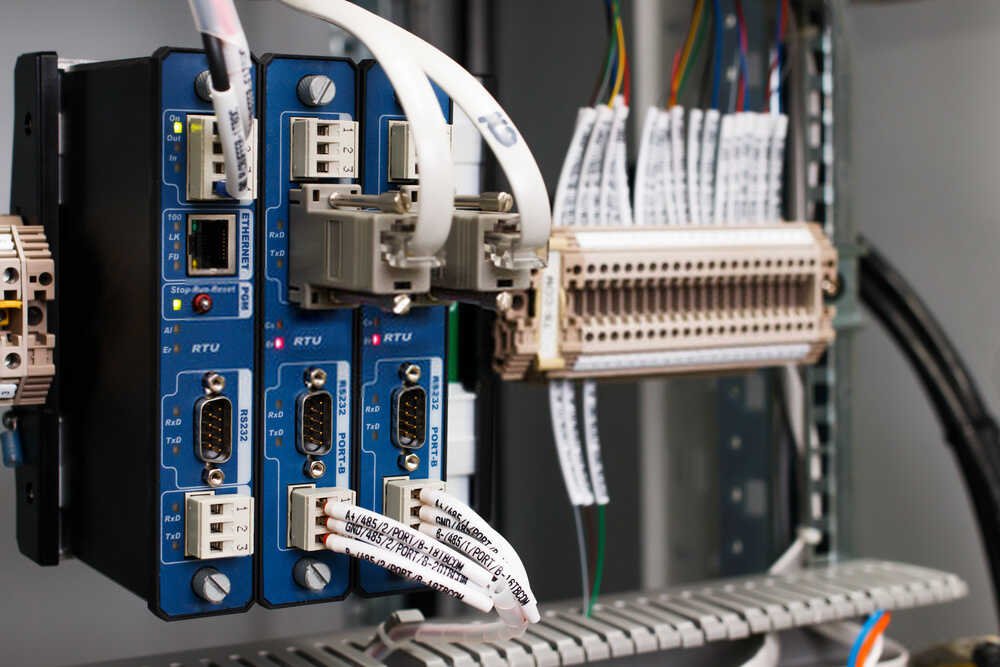
It’s rugged, it’s flexible, it’s smart, and it’s indispensable for so many industries some half-century after its inventor dreamed up the first PLC. That acronym stands for Programmable Logic Controller, which to many people looks like a ruggedized computer of some sort. And in a nutshell, that’s precisely what it is: a tough, industrialized box for all those visible inputs and outputs that house the all-important and powerful CPU. It’s fully programmable to execute the control instructions, communicate with other devices and networks, and carry out a series of daily tasks including diagnostics.
And in our rapidly advancing and ever-more-complex second decade of the 21st century, a programmable logic controller could well be the heart of so many of your own industry, business or organization’s most critical industrial processes going forward. That’s because our reliance on automated processes and machinery are multiplying exponentially year after year – whether we’re doing something as societally vital as generating electricity, making cars, steel, chemicals and keeping sewage systems running, to controlling how your hot water system and the air conditioner works.
You will find a programmable logic controller at the heart of:
Farming, for instance, to control livestock weight scales, milking machines and pesticide spraying machines.
Building safety, to control processes including air pressure regulation in the fire stairs of multi-story buildings.
Construction, for regulation of things like the mixing barrel on a cement machine.
The health, exercise & leisure industries, include treadmill operations, spa systems and floatation tanks, and amusement rides.
Mining, to monitor and measure iron ore quality, weight and composition and processing systems.
And so, so, so much more.
Without getting too deep into the weeds with complex technical jargon, the PLC works in a cyclical way based on four constantly recurring steps:
1. Input
Monitoring of the status and operation of any input device or devices connected to the PLC. These inputs may include switches and buttons, sensors and encoders.
2. Scan
Carries out the program logic that has been created by the PLC’s administrator.
3. Output
Either power up or power down any output devices connected to the PLC, such as valves, starter motors, alarms, horns, pumps, fans and actuators (and more).
Read Also: How Investing in Technology Can Save Your Business a Lot of Money
4. Housekeeping
Carries out communication processes and internal diagnostics, with steps 1-4 operating in a constant, sequential and continuous loop.
Not sure your application or operations require a PLC? Bear in mind that this evolving technology has been at the heart of automated processes for decades, for a huge list of reasons.
PLCs are:
* Easy to program in comparison to other industrial control systems.
* Affordable, with options ranging from basic models with accessible price points to highly complex units.
* Proven, after decades of profitable industrial use, exhaustive testing, deep analysis and research and constant technological evolution.
* Versatile, with even basic PLC models capable of integrating with very complex operations and systems.
* Durable and reliable in harsh environmental conditions, thanks in part to the solid-state design with no moving parts.
* With few components and no moving parts, PLCs are highly energy efficient.
Are you ready to choose the programmable logic controller that works best for your application or operations? Bear in mind that the product range is now impressively vast, meaning there’s much more to consider than just cost. You’ll need to match your PLC with your operation’s voltage requirements, software demands and CPU requirements, the number of inputs and outputs, communication and connectivity requirements and more.
As the smooth operation of your PLC will be critical to your most productive industrial operations, make sure you make the right choice of product by consulting with an experienced expert.